The body work is at a point where I can fit flares without worrying whether any part of the shell will be altered. Some time ago I had fitted the subframe, hubs & front rims to determine how far the wheels will stick out from the guard, which was measured as 42mm (with 0 degrees of camber) :


I sourced a set of fibreglass Wood and Pickett type flares which have a width of ~58mm (2.25") at the top of the arch.
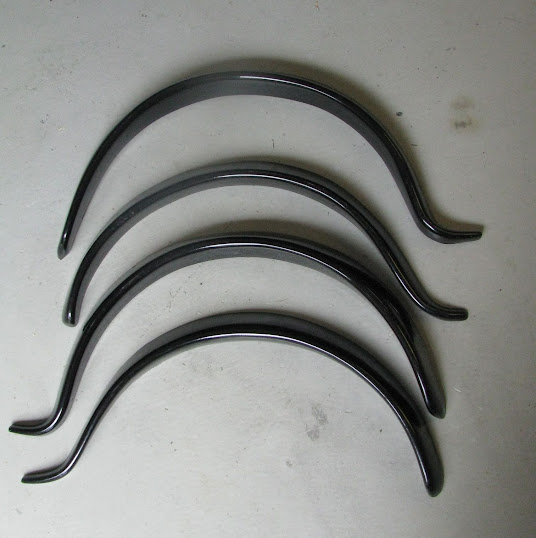
The flares were offered up to the shell and initially seemed like they all needed just a bit of work to butt up against the shell properly but that was the least of the problems. The flares didn't seem to match the curvature of the wheel arch lip. I scribed and cut some cardboard to the shape of the wheel arches to compare.

None of the four flares actually matched the wheel arch curves. For example this flare was okay at the top but tucked in at either end

compared to a set of (narrower) ABS plastic flares which matched the curve perfectly

To reshape the flares to match the wheel arch curvature I made a series of offset cuts along the length of each flare which allowed them to flex
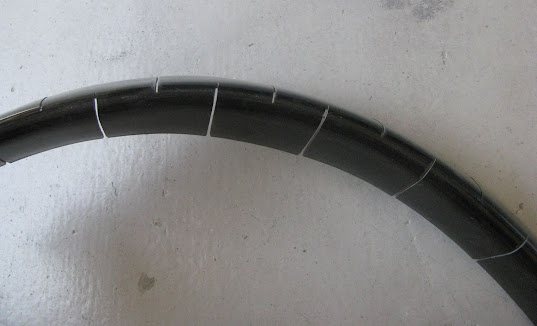
With the ends cut off this allowed me to clamp the flares to the body and superglue some small pieces of steel over the cuts to hold the corrected shape. A couple of layers of fibreglass was then applied to the back of the cuts.

The curve of the front flare lower section also did not match the body seam so this also had offset cuts to fit it
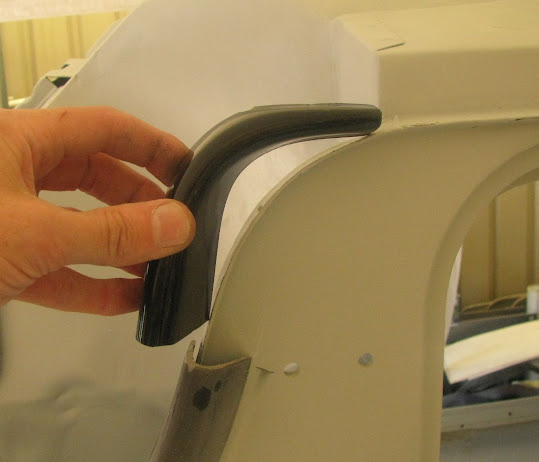

I had to extend the rear flares by approx 100mm to give it a more completed look with bumperless rear end. I formed a shape for the missing sections and these were then fibreglassed into the gap.
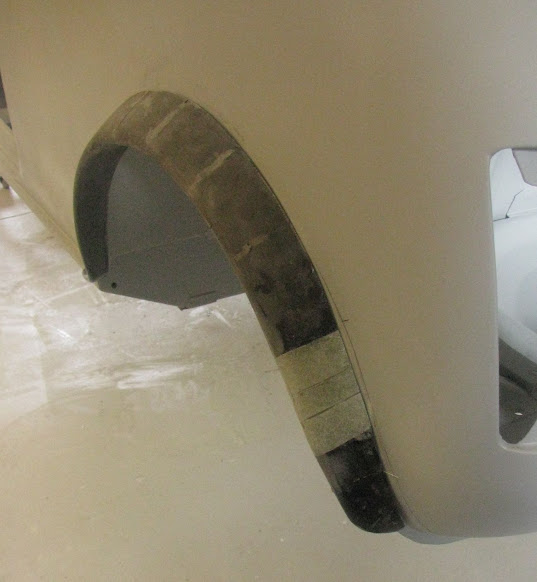
This style flare generally uses pop-rivets fitted from underneath, up into the wheel arch lips. I didn't like the idea of using pop-rivets to secure the flares as the wheel arch lip was as narrow as 8mm wide - not wide enough to be confident that they stay securely fitted so the lips were extended to approx 25mm
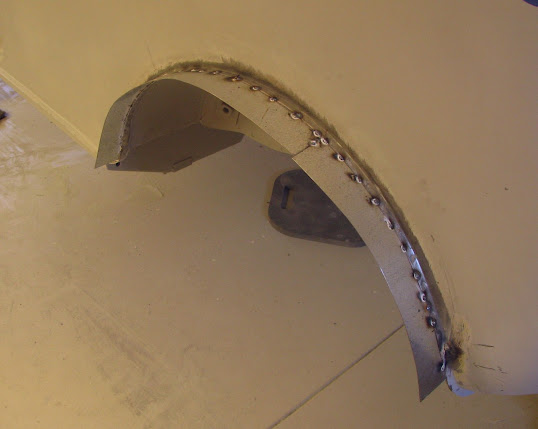
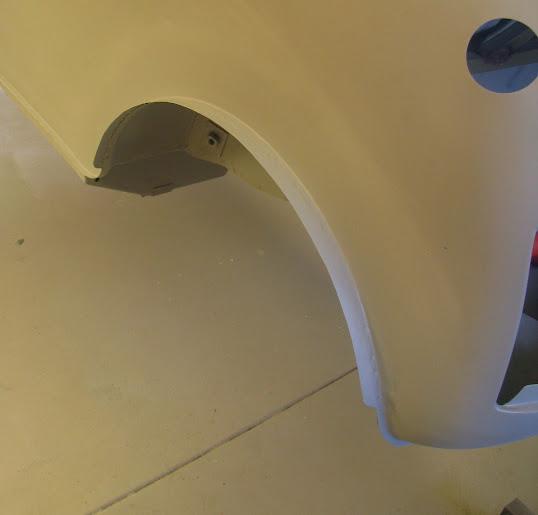
...then I welded on four M5 nuts on small plates for each flare to provide support for the thin-ish steel of the wheel lip extensions.

The flares then needed new fibreglass added to get them to butt up neatly against the body. I applied painters tape on the body to cover the panels and some fibreglass to bridge any gaps
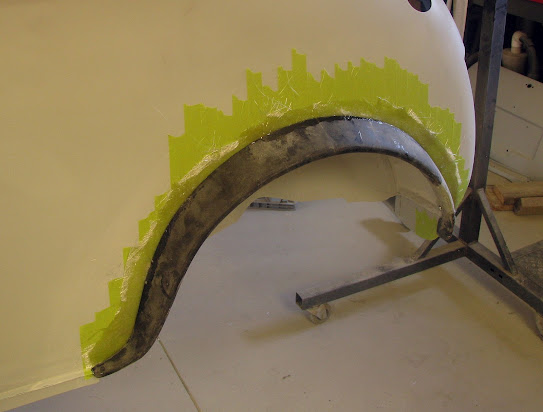
This took well over a month of detailed work (and lots of time waiting for fibreglass to cure) to get just the flares completed and fitting really well. So much for what I thought would be just a weekend or so of work bolting them on

_________________
-Alan
I blame my dad for my love of minis. I think I was conceived in the back seat of one
I also blame my Dad for me being 6' 1" - not really the optimum height for driving a Mini.