With the old etch primer and patches of spray can primer now removed from the Mini shell, more defects were exposed...
The curved panel section next to the rear wheel arch seam wasn't repaired well and had some pinholes so the panel was cut away and replaced (painted with black zinc paint before patching)
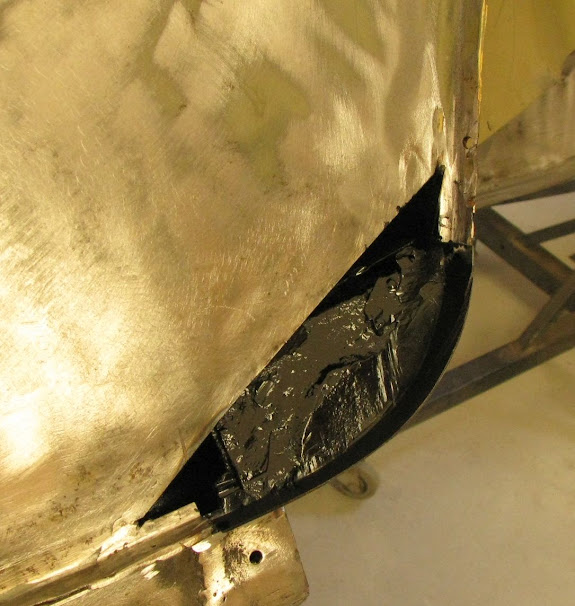
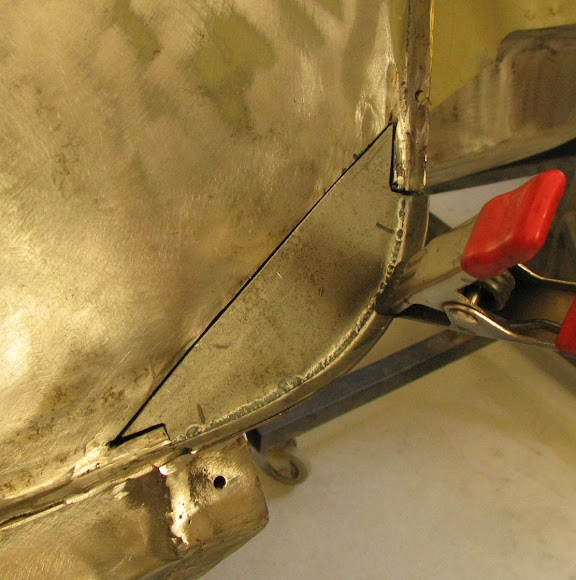
The drivers side wheel arch had an (attempted) repair which was just a glob of messy welds ... another patch
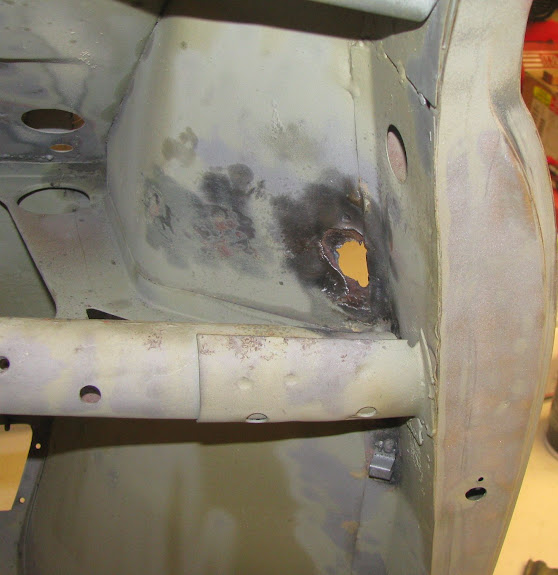
The passenger wheel arch had a couple of rust holes at the (very hard to reach) top corner of the wheel arch. I cut an access hole next to the door to investigate and found multiple rust holes large enough to stick a 12mm drill bit through (Torch shining through from the wheel arch in this pic)

After removing the outer & inner A-panels it exposed a huge section of rust damage that had never been repaired properly - just a piece of steel welded over it. There is supposed to be a vertical panel here, not a gaping rusty hole

After the couple of gussets in the upper wheel arch had the spot welds drilled out and removed, it revealed a massive rust hole that was hiding behind them. I'm super glad I wanted to go to the effort of fixing this - it would have rusted out again in no time after driving in any wet weather.

More patches...
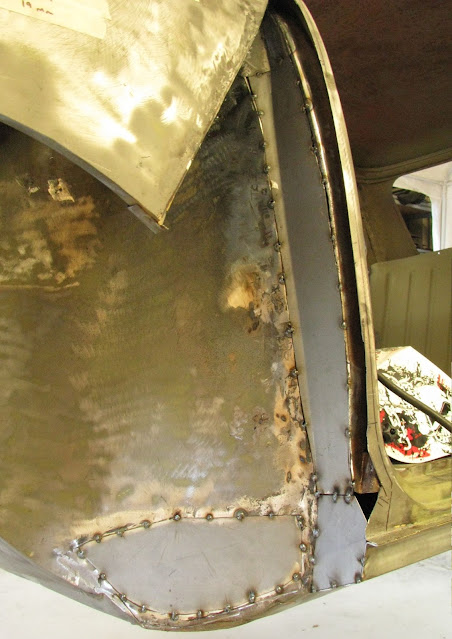
Some 3D prints which matched the external hinge hole positions exactly were bolted to the door. These hinge prints allowed me to determine the exact position required by the A panels by aligning the holes in the prints with the holes in the new A-pillar panels.

Much trimming, tweaking and panel beating later, the new A-pillar panels were welded in

A repair patch had also been welded in the drivers side front wheel arch and given the low quality of repairs I'd already found, I cut this patch off... and found yet another example of a steel piece just welded over the top of rust damage.

This was fixed after treating the rust behind the wheel arch with zinc paint. I welded in some new steel - correctly this time which includes the way the separate inner A-panel is supposed to wrap under the sill.

So that completes all rust repairs and fixing previous shoddy repairs (Am I jinxing myself here?). Now onto the next stage of bodywork and panel alignment.
_________________
-Alan
I blame my dad for my love of minis. I think I was conceived in the back seat of one
I also blame my Dad for me being 6' 1" - not really the optimum height for driving a Mini.